GO Back
To provide exposure to the students with hands on experience on various basic engineering practices in Civil, Mechanical, Electrical and Electronics Engineering.
On successful completion of this course, the student will be able to fabricate carpentry components and pipe connections including plumbing works.
use welding equipments to join the structures.
Carry out the basic machining operations
Make the models using sheet metal works
Illustrate on centrifugal pump, Air conditioner, operations of smithy, foundary and fittings
To Study and practise various operations that can be performed in lathe, shaper, drilling, milling machines etc. and to equip with the practical knowledge required in the core industries
CO1: Demonstrate the safety precautions exercised in the mechanical workshop.
CO2: Make the workpiece as per given shape and size using Lathe.
CO3: Join two metals using arc welding.
CO4: Use sheet metal fabrication tools and make simple tray and funnel.
CO5: Use different moulding tools, patterns and prepare sand moulds.
To verify the principles studied in Fluid Mechanics theory by performing experiments in lab.
Upon completion of this course, the students will be able to:
Use the measurement equipments for flow measurement.
Perform test on different fluid machinery.
To study the mechanical properties of materials when subjected to different types of loading.
To verify the principles studied in Fluid Mechanics theory by performing experiments in lab.
Ability to perform Tension, Torsion, Hardness, Compression, and Deformation test on Solid materials.
To study the value timing-V diagram and performance of IC Engines
To Study the characteristics of fuels/Lubricates used in IC Engines
To study the Performance of steam generator/ turbine
To study the heat transfer phenomena predict the relevant coefficient using implementation
To study the performance of refrigeration cycle / components
CO1: conduct tests on heat conduction apparatus and evaluate thermal conductivity of materials.
CO2: conduct tests on natural and forced convective heat transfer apparatus and evaluate heat transfer coefficient.
CO3: conduct tests on radiative heat transfer apparatus and evaluate Stefan Boltzmann constant and emissivity.
CO4: conduct tests to evaluate the performance of parallel/counter flow heat exchanger apparatus and reciprocating air compressor.
CO5: conduct tests to evaluate the performance of refrigeration and airconditioning test rigs.
To familiar with different measurement equipments and use of this industry for quality inspection.
CO1: Measure the gear tooth dimensions, angle using sine bar, straightness and flatness, thread parameters, temperature using thermocouple, force, displacement, torque and vibration.
CO2: Calibrate the vernier, micrometer and slip gauges and setting up the comparator for the inspection.
To supplement the principles learnt in kinematics and Dynamics of Machinery.
To understand how certain measuring devices are used for dynamic testing.
CO1: Explain gear parameters, kinematics of mechanisms, gyroscopic effect and working of lab equipments.
CO2: Determine mass moment of inertia of mechanical element, governor effort and range sensitivity, natural frequency and damping coefficient, torsional frequency,critical speeds of shafts, balancing mass of rotating and reciprocating masses, and transmissibility ratio.
To know the method of programming the microprocessor and also the design, modeling & analysis of basic electrical, hydraulic & pneumatic Systems which enable the students to understand the concept of mechatronics.
CO1: Demonstrate the functioning of mechatronics system with various pneumatic, hydraulic and electrical systems.
CO2: Demonstrate the functioning of control systems with the help of PLC and microcontrollers.
To gain practical experience in handling 2D drafting and 3D modelling software systems.
To study the features of CNC Machine Tool.
To expose students to modern control systems (Fanuc, Siemens etc.,)
To know the application of various CNC machines like CNC lathe, CNC Vertical Machining centre, CNC EDM and CNC wire-cut and studying of Rapid prototyping.
To give exposure to software tools needed to analyze engineering problems.
To expose the students to different applications of simulation and analysis tools.
CO1: Draw 3D and Assembly drawing using CAD software
CO2: Demonstrate manual part programming with G and M codes using CAM
CO1: simulate the working principle of air conditioning system, hydraulic and pneumatic cylinder and cam follower mechanisms using MATLAB.
CO2: analyze the stresses and strains induced in plates, brackets and beams and heat transfer problems.
CO3: calculate the natural frequency and mode shape analysis of 2D components and beams.
- ENGINEERING PRACTICES LABORATORY
- MANUFACTURING TECHNOLOGY LABORATORY
- FLUID MECHANICS AND MACHINERY LABORATORY
- STRENGTH OF MATERIALS LABORATORY
- THERMAL ENGINEERING LABORATORY
- METROLOGY & MEASUREMENTS LABORATORY
- DYNAMICS LABORATORY
- MECHATRONICS LABORATORY
- CAD/CAM LABORATORY
- AUTOMATION AND METAL FORMING LABORATORY
ENGINEERING PRACTICES LABORATORY
Objectives
Outcomes
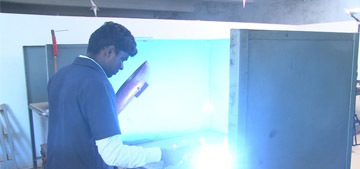
MANUFACTURING TECHNOLOGY LABORATORY
Objectives
Outcomes
Upon the completion of this course the students will be able to
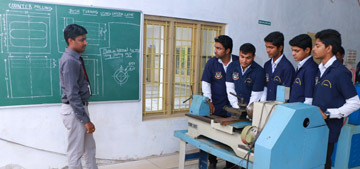
FLUID MECHANICS AND MACHINERY LABORATORY
Objectives
Outcomes
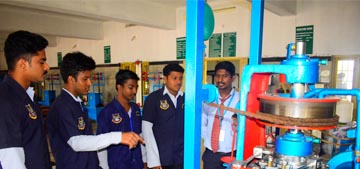
STRENGTH OF MATERIALS LABORATORY
Objectives
Outcomes
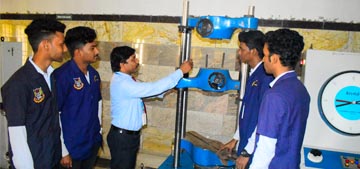
THERMAL ENGINEERING LABORATORY
Objectives
Outcomes
Upon the completion of this course the students will be able to
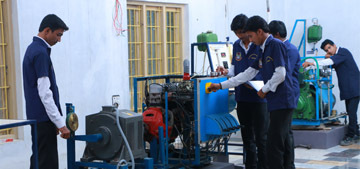
METROLOGY & MEASUREMENTS LABORATORY
Objectives
Outcomes
Upon the completion of this course the students will be able to
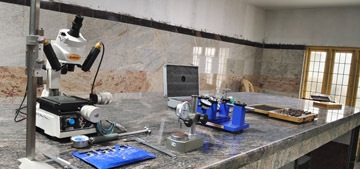
DYNAMICS LABORATORY
Objectives
Outcomes
Upon the completion of this course the students will be able to
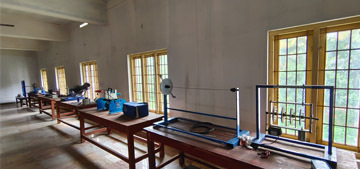
MECHATRONICS LABORATORY
Objectives
Outcomes
Upon the completion of this course the students will be able to
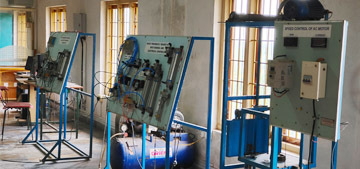
CAD/CAM LABORATORY
Objectives
Outcomes
Upon the completion of this course the students will be able to
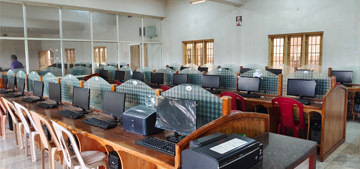
AUTOMATION AND METAL FORMING LABORATORY
Objectives
- 1) To train the students on the basic concepts of metal forming processes
- 2) To determine metal forming parameters for a given shape
- 3) To learn the automation systems using fluid power control systems
- 4) To learn and use automation studio software
- 5) To learn PLC and its importance in Fluid power applications
Outcomes
- At the end of this course the students are expected
- 1) To impart practical knowledge on bulk metal forming processes
- 2) Know various symbols used in Hydraulic and Pneumatic circuits
- 3) Conduct few sheet metals forming processes and analyse the parameters
- 4) Design hydraulic circuits for industrial applications
- 5) Learnt how to use automation studio